5 Reasons Why You Should Start Using Prekitting, by Televend
Do you want to know how to serve up to twice as many machines per day? Or how to decrease your fuel costs and vehicle vandalism? The answer is prekitting.
What is prekitting?
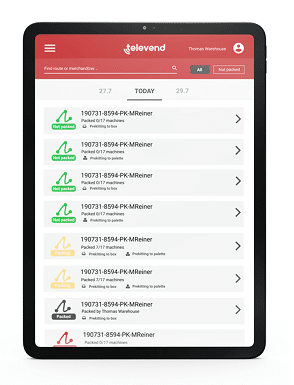
We all know what the standard service machine visit looks like. Fillers need to check a machine first to see what is missing, then go to the van to pick up the missing products, and finally return to the machine with the products. To compensate for the time of making an extra trip to the machine, they take too much load with them and then additional time to return extra products to the van.
With the prekitting system, however, the whole process is simplified and cost-saving. Prekitting is the process of preparing the products necessary to fill machines for each location in advance. It is based on real-time sales data collected from the machines and processed by a vending management system (VMS).
How does it work? The prekitting system receives information from VMS about stock sold out at the machines. Then it sends an order to warehouse workers with the exact inventory needed for each machine the following day. The workers can see the order via the wireless displays installed in the warehouse, light bulbs on shelves that indicate which items to pick, or a tablet app.
Eliminate manual product count
On average, it takes service operators 30 minutes to restock each machine, with an average of 12-14 machines serviced in a single business day.
With prekitting, you can eliminate the need for manual count on every service, as you know how much stock is left in the machine before you visit it. This reduces the duration of the service visits by 50%, resulting in 18-21 machines being serviced daily.
Service up to 40% more machines
The standard machine refill includes loading the van as much as possible with the stock, then going to the location and pulling out the products from the truck several times until the machine is full. On average, 40-50% of the driver’s day is spent pulling out the products from the truck.
With a prekitting system, the stock is prearranged into boxes for each machine. The drivers can just take out the box and fill the machine with the products straightway and eliminate unnecessary on-site activities.
Streamline warehouse processes
You can arrange your warehouse space to streamline the entire process and pack even faster. For example, you can store the products according to the machine’s planogram – place them in the warehouse to reflect their position in the machine. You can also optimize the packing area, loading area, and so on to minimize the number of unnecessary activities.
Moreover, with prekitting, you can simultaneously pack products for multiple machines and save valuable time going back and forth through the warehouse.
Decrease van load by up to 60%
Since drivers didn’t know how much stock they needed to refill the machines, they would overstock the van and then decide on the spot which products they needed. They used the van as a temporary storage room.
With prekitting, that is not the case. By transporting the exact quantities of products to restock the machines, you can lower the weight of the load in the vans. That means you can use smaller, lighter trucks, and consequently, you can reduce fuel costs.
Reduce product spoilage and theft
With the old system, not all products would be restocked, and vans would be full of leftover items at the end of the shift – sometimes even overnight. That is crucial for products with short shelf life because they could get spoiled if left in the van for an extended period. On top of that, products left overnight without supervision are a huge theft risk.
Having the prekitting system in place and knowing the exact quantity of products for a refill means you don’t have any stock left to return to the warehouse. The trucks are full in the morning and empty at the end of the day. That eliminates both product spoilage and theft.
How to prekit with Televend
Televend is the vending management system that collects real-time stock data from your machines and streamlines warehouse processes. It includes a back-office cloud app instructing what products should be packed, a tablet app for warehouse workers, and a mobile app for service drivers with refill jobs for each day.
The vending management cloud app collects real-time stock data from the machines and creates a list for warehouse workers every evening for the following day. It even forecasts the pickup values for fast-selling products using a smart AI algorithm, so you can predict how many products you will sell on a suggested day.
Warehouse workers get an instant overview of packing jobs for each day on their prekitting tablet app. Depending on the machine type and route, they can choose between the following:
- Pre-Kitting to box – pack products for each individual machine into boxes. To speed up the packing, you can pack up to five machines at once by putting several boxes on the cart.
- Pre-Kitting to Pallets – pack the products for multiple machines onto one pallet.
Status indicates routes that need to be packed, are currently being packed, finished packing, and overdue routes.
ach box they pack gets a unique bar code which they can scan when loading them into a van so that they can arrange them logically – first in, last out. When they arrive at the site, drivers can also scan the box with their vending service mobile app to be sure they have the right products and do their job as efficiently as possible.
If you want to learn more about how Televend can help you, schedule a demo with our product experts.